In today’s digital age, cable assembly projects play a crucial role in ensuring seamless connectivity across various devices and systems. Whether it’s for audio and video systems, telecommunications, or power transmission, choosing the right connectors is essential for the success of your cable assembly projects. This article will guide you through the process of selecting connectors, understanding their types, factors to consider, installation, and troubleshooting common issues.
Understanding Cable Assembly Projects
Basics of Cable Assembly
Before delving into the world of connectors, it is essential to have a basic understanding of cable assembly. Cable assembly projects involve the integration of cables, wires, connectors, and related components to create a unified system for transmitting data, signals, or power. It is crucial to ensure that the connectors used in these projects are compatible, reliable, and meet the specific requirements of the application.
Importance of Connector Selection in Cable Assembly
The selection of connectors plays a vital role in the overall performance and reliability of cable assembly projects. A well-chosen connector ensures seamless transmission of signals or power with minimal loss, interference, or degradation. Additionally, connectors should provide a secure and durable connection to avoid potential disruptions and maintain signal integrity. Therefore, understanding the different types of connectors available is paramount.
Types of Connectors for Cable Assembly
RF Connectors
RF (Radio Frequency) connectors are widely used in the telecommunications and broadcasting industries. These connectors are designed to transmit high-frequency signals with minimal loss. Common RF connectors include BNC, SMA, and F-Type connectors. When selecting RF connectors, factors such as impedance matching and signal integrity become critical to ensure reliable transmission.
Audio and Video Connectors
For audio and video applications, connectors such as RCA, XLR, and HDMI are commonly used. These connectors ensure clear and high-quality signal transmission between audio/video equipment. When choosing audio and video connectors, factors like signal fidelity, compatibility, and shielding capabilities should be considered to achieve optimal performance.
Power Connectors
Power connectors are designed to transmit electrical power between devices or systems. They come in various types, such as barrel connectors, AC/DC power connectors, and power cords with different plug configurations. When selecting power connectors, factors such as current rating, voltage compatibility, and safety standards should be carefully evaluated to ensure efficient power transfer and prevent any potential hazards.
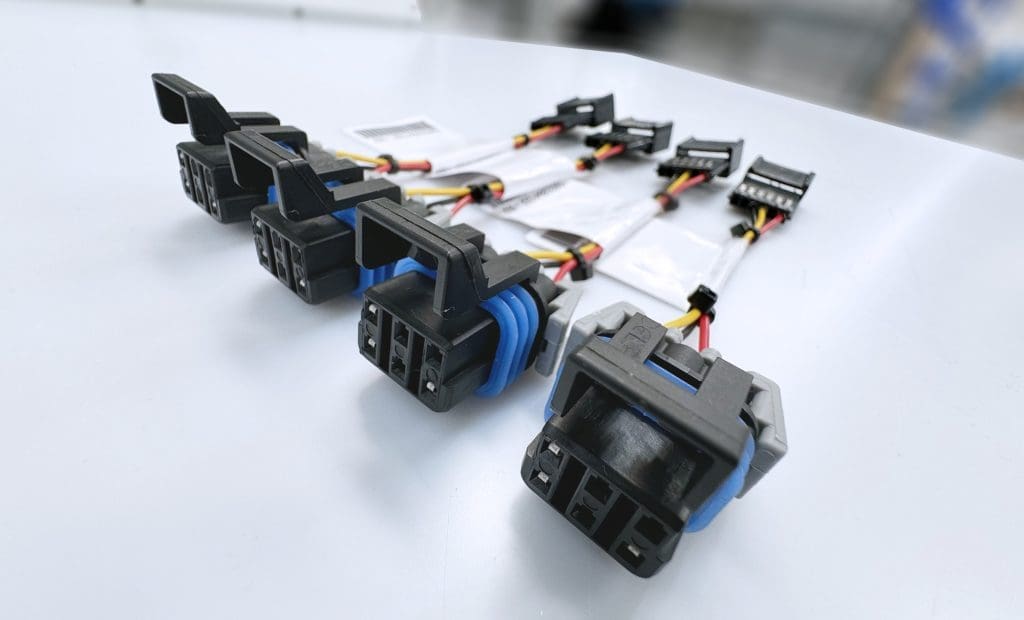
Factors to Consider When Choosing Connectors
Material and Quality
The material and quality of connectors are crucial for their performance and longevity. Connectors made from high-quality materials, such as corrosion-resistant metals or durable plastics, ensure reliability and prevent premature failure. It is essential to choose connectors from reputable manufacturers with a track record of producing high-quality products that meet industry standards.
Connector Size and Shape
The size and shape of connectors impact the ease of installation and the space required in cable assembly projects. Choosing connectors of appropriate size ensures compatibility with existing equipment and provides a secure and snug fit, minimizing the risk of connectivity issues. It is also important to consider the physical constraints of the application, such as tight spaces or environmental conditions, to choose connectors that can withstand these challenges.
Connector Performance
Connector performance refers to factors such as signal integrity, impedance matching, and transmission efficiency. Before finalizing connector selection, it is crucial to evaluate various performance parameters to ensure optimal performance and avoid potential signal degradation or interference. Consulting technical specifications and seeking expert advice can help in selecting connectors that meet the specific requirements of your cable assembly projects.
Connector Installation and Maintenance
Proper Installation Techniques
Proper installation techniques are essential to ensure the longevity and reliability of connectors. This includes correctly aligning and inserting connectors, securely fastening them, and following recommended installation practices. It is important to avoid over or under-tightening connectors, as this can lead to loss of signal integrity or damage to the connectors or the cable assembly itself. Following manufacturer guidelines and industry best practices is crucial for successful connector installation.
Maintaining Your Connectors for Longevity
Maintaining connectors is crucial to extend their lifespan and prevent performance degradation. Regular cleaning of connectors and inspection for damage or wear can help identify potential issues early on. Proper storage and protection of connectors from dust, moisture, and physical damage also contribute to their longevity. Additionally, periodic checks and retermination of connectors may be necessary to maintain optimal performance over time.
Troubleshooting Common Connector Issues
Dealing with Loose Connections
Loose connections can result in intermittent or poor signal transmission. To address this issue, ensure that the connectors are properly tightened and securely fastened. Inspecting the connectors for any signs of wear, corrosion, or damage and replacing them if necessary can help restore a stable connection. Using locking mechanisms or strain relief techniques can also prevent connectors from becoming loose due to movement or external factors.
Overcoming Corrosion and Wear
Corrosion and wear are common issues that can affect connector performance over time. To mitigate the effects of corrosion, connectors with corrosion-resistant plating or materials should be selected. Regular cleaning and inspection of connectors can help identify and address any signs of corrosion or wear early on. Additionally, using protective measures such as weatherproofing or implementing proper environmental controls can prevent avoidable damage to connectors.
Frequently Asked Questions
Q: Can I interchange connectors from different manufacturers?
A: While some connectors may have similar form factors, it is generally recommended to use connectors from the same manufacturer or ones that are certified to be compatible. Different manufacturers may have variations in pin configurations, impedance matching, or tolerances that can affect the performance of the cable assembly system.
Q: Can I reuse connectors in different projects?
A: Reusing connectors depends on various factors, such as the condition of the connectors, their compatibility with the new project’s requirements, and the risk of potential performance degradation. It is advisable to consult with experts or manufacturers to determine if reusing connectors is safe and suitable for your specific application.
Q: Is it necessary to use connectors with gold plating?
A: Gold plating on connectors can enhance their performance by improving conductivity, minimizing corrosion, and reducing signal loss. However, the necessity of gold plating depends on the specific application and its requirements. In some cases, connectors with gold plating may be essential, while in others, alternative plating options or materials may suffice.
Q: How often should I inspect and clean the connectors?
A: Regular inspection and cleaning of connectors are recommended to prevent dust, debris, and corrosion buildup. How often this should be done depends on various factors, such as environmental conditions, frequency of use, and the criticality of the application. As a general guideline, connectors should be inspected and cleaned at least once every six months, or more frequently if they are exposed to harsh environments or heavy usage.
Q: What should I do if I encounter compatibility issues with connectors?
A: If you encounter compatibility issues with connectors, it is advisable to consult with the manufacturer or seek expert advice. They can provide guidance on alternative connector options, adapters, or other solutions that can resolve compatibility problems without compromising the performance or reliability of the cable assembly system.
Choosing the right connectors is critical to the success of your cable assembly projects. By understanding the basics of cable assembly, exploring the different types of connectors, considering key factors, and following proper installation and maintenance practices, you can ensure optimal performance and longevity of your cable assembly systems. In case of any doubts or challenges, do not hesitate to reach out to experts or consult reputable manufacturers to make informed decisions.
When it comes to ensuring the success of your cable assembly projects, the expertise and quality that Cornelius Electronics brings to the table are unparalleled. With over four decades of experience in the industry, our UK-based team at Cornelius Electronics is dedicated to providing you with the highest quality wiring harnesses, cable assemblies, box builds, and system integration services. Our 50,000 square foot facility and 250 trained operatives are at the forefront of creating partnership-focused solutions tailored to your needs. For controlled, repeatable volumes of high-quality components, look no further. Get in touch with us today to see how we can contribute to the success of your cable assembly projects.